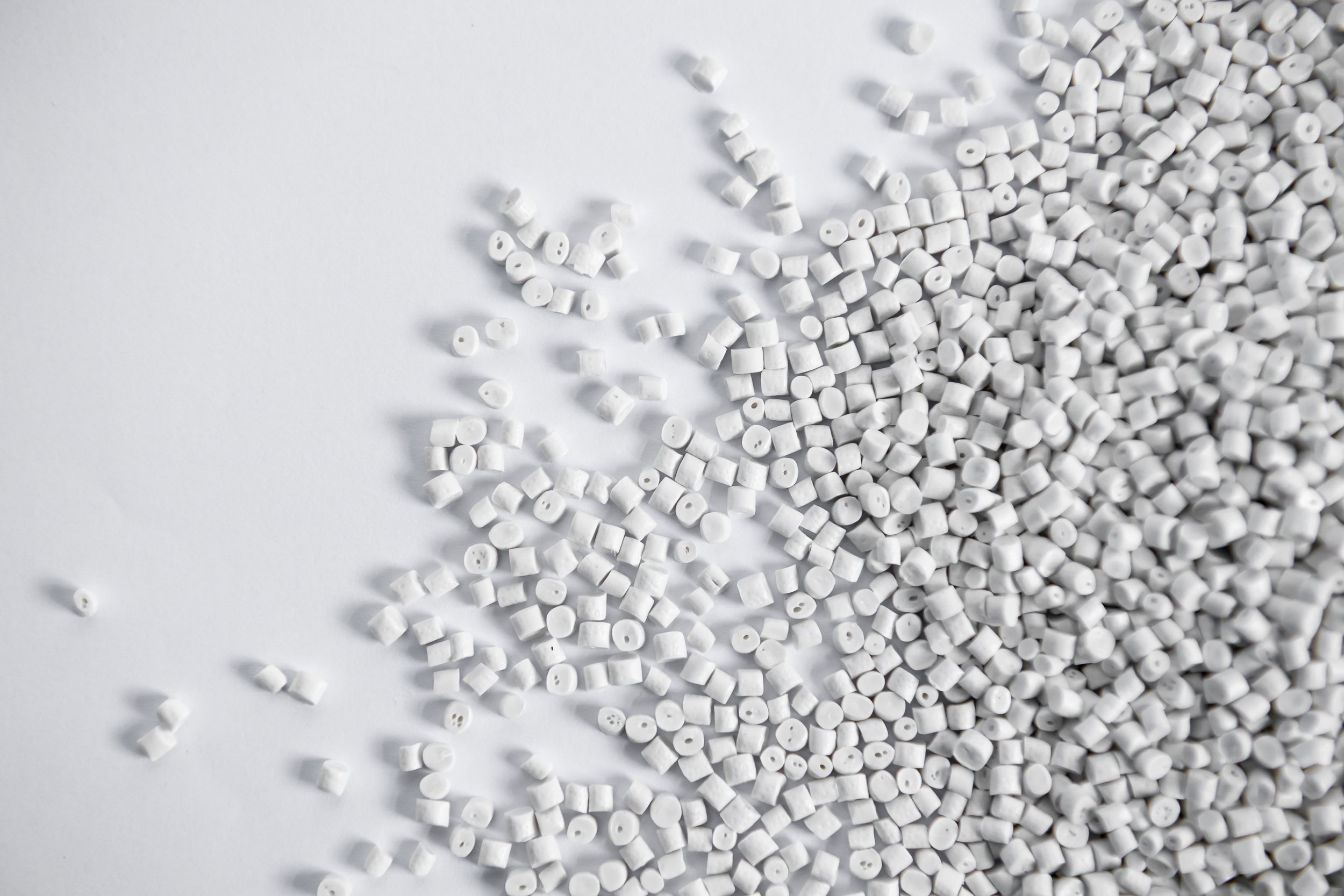
Acrylonitrile Butadiene Styrene (ABS) & The Injection Moulding Process.
Acrylonitrile Butadiene Styrene (ABS) is a highly popular thermoplastic used in injection molding due to its excellent balance of mechanical properties and processability. Below are some of its unique properties:
1. High Impact Strength
ABS has exceptional toughness and impact resistance, making it ideal for products that must withstand mechanical stress and shock. This property is particularly useful for automotive components, protective gear, and durable consumer goods.
2. Good Heat Resistance
ABS can withstand moderate temperatures without deforming, with typical heat deflection temperatures around 80-100°C. This makes it suitable for applications where heat resistance is required, such as appliance housings and electronics.
3. Excellent Surface Finish
ABS produces a high-quality surface finish in the injection molding process, often glossy and smooth. This makes it ideal for products that require a polished appearance or will undergo further finishing, like painting or chrome plating.
4. Good Dimensional Stability
ABS maintains its shape and size well over time and under varying environmental conditions. This is critical for precision parts that need to maintain tight tolerances, such as electronics enclosures or automotive components.
5. Easy to Process
ABS is highly moldable and can flow into complex molds easily, which reduces cycle times and increases manufacturing efficiency. Its relatively low melting point (around 200°C) allows for quicker production without compromising the strength of the final product.
6. Customizability
ABS can be modified with additives to improve specific properties, such as increased UV resistance, enhanced flame retardancy, or improved strength, making it adaptable to various applications.
7. Chemical Resistance
ABS is resistant to many acids, alkalis, and oils, making it suitable for products that might encounter chemicals or cleaning agents, such as appliance housings, plumbing components, and automotive parts.
8. Electrical Insulating Properties
ABS is a good electrical insulator, which makes it suitable for electronic housings, connectors, and other electrical components that require resistance to electrical conductivity.
9. Lightweight
Although it is durable and tough, ABS is still relatively lightweight, which helps in applications where weight reduction is important, such as automotive parts and portable electronics.
10. Good Machinability
ABS is easily machinable, meaning it can be processed further after molding (e.g., drilling, sanding, or cutting), which adds to its versatility for custom applications.
11. Resistant to Abrasion
ABS has good resistance to abrasion, making it ideal for applications that involve friction or wear, such as gears, mechanical components, and moving parts.
12. Low Shrinkage
ABS has relatively low shrinkage during the cooling phase of injection molding, which results in more dimensionally accurate parts and reduces the likelihood of warping or deforming.
13. Wide Range of Colors
ABS can be easily colored during the injection molding process, making it suitable for consumer products that require specific aesthetic qualities without the need for post-mold painting.
14. Good Adhesion to Paints and Platings
ABS is highly compatible with surface treatments such as painting, electroplating, or even vacuum metallization. This property makes it an ideal choice for aesthetic parts that require additional finishing, such as automotive interior components or high-end consumer electronics.
15. Recyclability
Like many thermoplastics, ABS is recyclable, which helps reduce material waste and improve sustainability.
These properties make ABS a versatile and popular material in industries such as automotive, electronics, toys, and consumer goods.