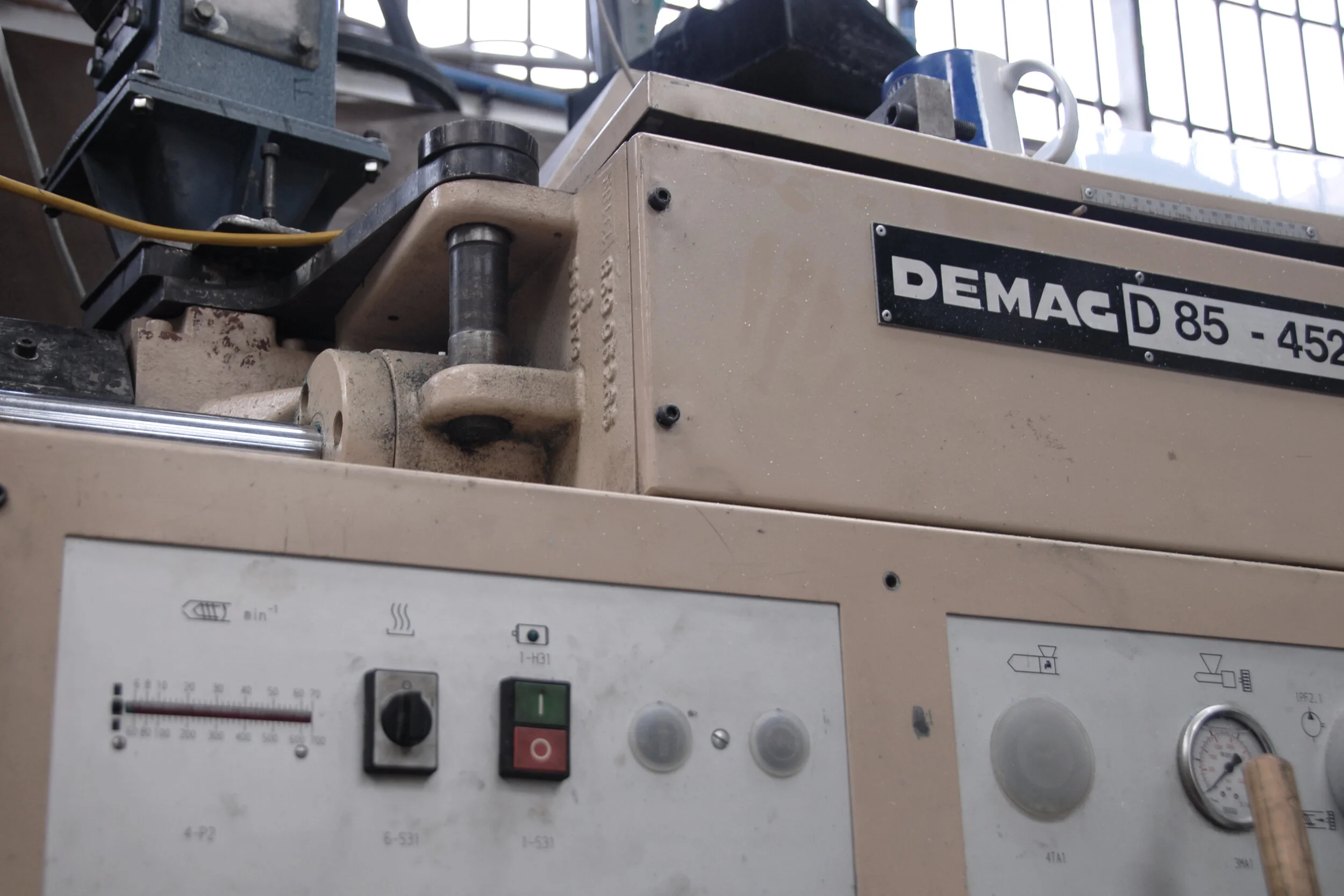
5 Plastics Commonly Used in Plastic Injection Molding
Injection molding is a popular manufacturing process for producing a wide variety of parts, from small components to large complex items. Central to this process are the plastics used, each offering unique properties that make them suitable for different applications. Here are five of the most commonly used plastics in injection molding:
1. Polypropylene (PP)
Properties:
- High Flexibility: Polypropylene is known for its ability to bend without breaking.
- Chemical Resistance: It resists many chemicals, making it ideal for use in laboratory equipment.
- Low Density: This plastic is lightweight, reducing the overall weight of the final product.
Applications:
Automotive parts, reusable containers, medical devices, and household goods.
2. Acrylonitrile Butadiene Styrene (ABS)
Properties:
- High Impact Resistance: ABS is tough and can withstand impacts, making it perfect for durable goods.
- Good Dimensional Stability: It holds its shape well during and after the molding process.
- High Surface Quality: This plastic is often used when a glossy finish is required.
Applications:
LEGO bricks, electronic housings, automotive parts, and consumer products.
3. Polycarbonate (PC)
Properties:
- Transparency: Polycarbonate is clear, allowing for light transmission similar to glass.
- High Strength: It is very strong and resistant to impact and fracture.
- Thermal Resistance: PC can withstand high temperatures, making it suitable for heat-prone environments.
Applications:
Optical discs, eyewear lenses, automotive headlamps, and electronic components.
4. Nylon (Polyamide, PA)
Properties:
- **High Wear Resistance:** Nylon is durable and resistant to abrasion, ideal for mechanical parts.
- **Low Friction Coefficient:** It reduces friction, which is beneficial in moving parts.
- **Good Chemical Resistance:** This plastic can resist various chemicals, enhancing its longevity in harsh environments.
Applications:
Gears, bearings, bushings, and automotive parts.
5. Polyethylene (PE)
Properties:
- Versatility: Available in various densities (LDPE, HDPE), each offering different properties.
- Moisture Resistance: PE is highly resistant to moisture, making it suitable for packaging.
- Flexibility: It can be both flexible and rigid, depending on the density used.
Applications:
Plastic bags, containers, bottles, and toys.
The team at S.B. Weston have a great deal of experience in choosing materials according to the specific requirements of a project, taking into consideration important properties of the required part such as durability, flexibility, chemical resistance, and cost.
Each of the five common plastics mentioned in this blog post offers unique advantages, making any one of them suitable for a wide range of products in various industries.
We can assist you in understanding their properties and in making an informed decision when selecting the material to manufacture in so that parts of the highest-quality are produced as efficiently, and as cost-effectively as possible.
Contact S.B. Weston for Expert Plastic Injection Mold Advice
Why not get in touch and arrange a free, no obligation design consultation where members of our experienced team can look at your project’s exact requirements and advise you how to best proceed. We’re happy to sign NDA’s to protect your product designs, so why not get in touch, we’d love to help make your project a British manufacturing success!