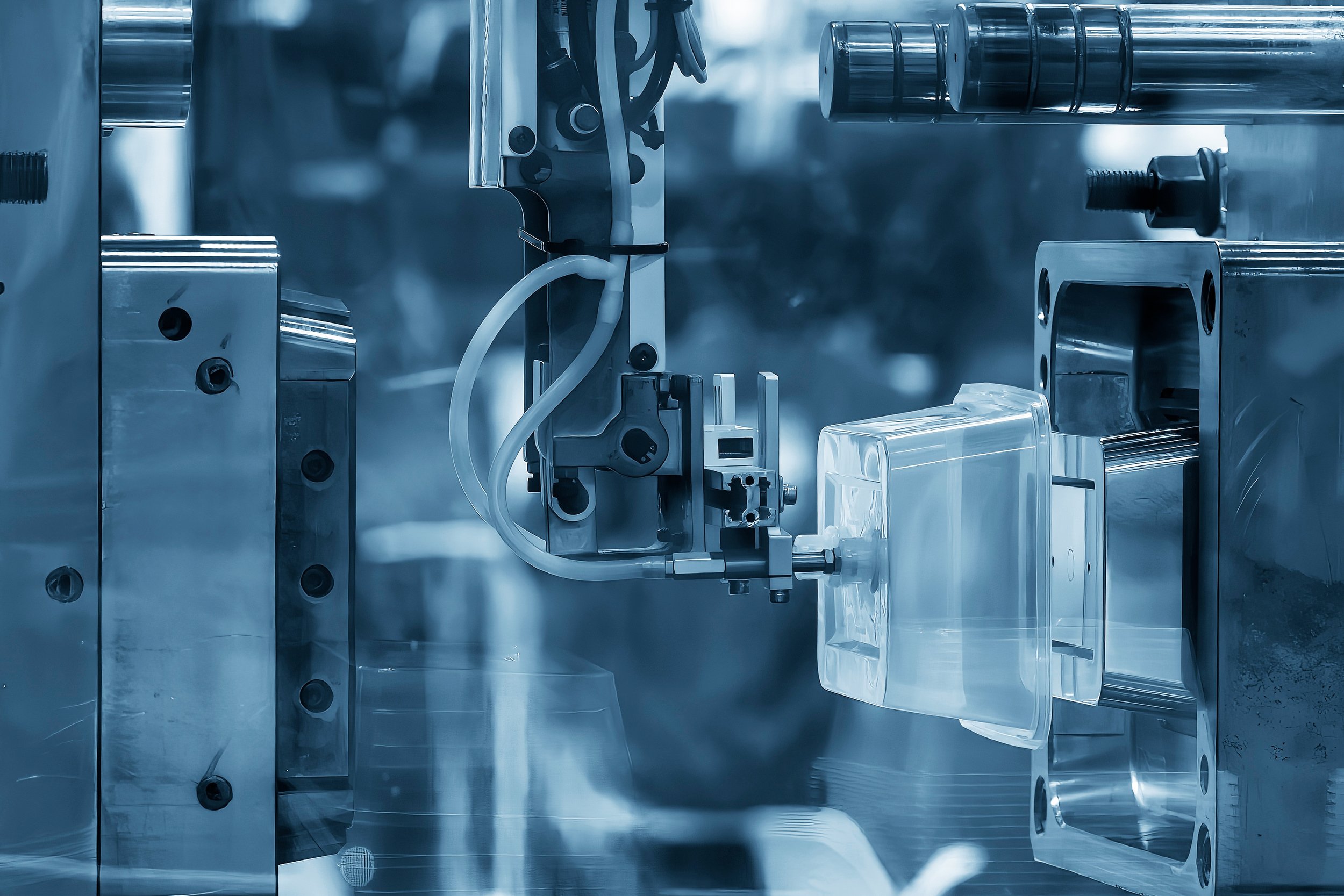
Understanding Plastic Injection Molding.
At S.B.Weston, we specialise in plastic injection molding, a widely used manufacturing process for producing a variety of plastic parts. From everyday items like bottle caps and toys to complex automotive components, this technique offers precision, efficiency, and versatility. Here's a closer look at how the injection molding process works.
What Happens During the Injection Molding Process?
Injection Molding is a manufacturing process in which molten plastic is injected into a mold cavity, where it cools and hardens to the shape of the mold. This process is highly efficient for mass production of identical parts with tight tolerances.
Key Steps in the Injection Molding Process
1. Clamping
The process begins with the clamping of the mold. The mold is typically made of two halves: the cavity and the core. These halves are held together by a clamping unit, ensuring they stay securely closed during the injection process.
2. Injection
Plastic pellets are fed into the injection molding machine via a hopper. These pellets are then heated to a molten state and injected into the mold cavity through a nozzle and runner system. The injection speed and pressure are carefully controlled to ensure the material fills the entire mold cavity.
3. Cooling
Once the molten plastic fills the mold, it begins to cool and solidify. Cooling channels within the mold help to speed up this process by circulating coolant, usually water, around the mold. Proper cooling is essential to maintain the integrity and dimensional accuracy of the part.
4. Ejection
After the part has cooled sufficiently, the mold opens, and an ejection system pushes the part out of the mold cavity. Ejector pins or plates are commonly used to release the part without damaging it.
5. Finishing
The final step involves any necessary post-processing, such as trimming excess material (flash), painting, or assembling multiple components. Some parts may require additional quality checks to ensure they meet specifications.
Advantages of Injection Molding as a Manufacturing Process
1. High Efficiency: Once the initial setup is complete, the production process is extremely fast, making it ideal for high-volume manufacturing.
2. Precision and Consistency: Injection Molding produces parts with high precision and repeatability, ensuring consistent quality across large production runs.
3. Material Versatility: A wide range of thermoplastic and thermosetting polymers can be used, allowing for diverse applications.
4. Complex Geometries: Intricate designs and complex shapes can be easily produced with the right mold design.
Applications of Injection Molding
Injection Molding is used across various industries, including:
- Automotive: Manufacturing components like dashboards, bumpers, and interior panels.
- Consumer Goods: Producing items such as containers, toys, and electronic housings.
- Medical: Creating medical devices, syringes, and surgical instruments.
- Packaging: Making caps, closures, and packaging containers.
Is Injection Molding the Correct Manufacturing Process for Your Project?
Injection Molding is a highly efficient and versatile manufacturing process that plays a critical role in producing a wide array of plastic parts. Its ability to produce high-quality, consistent parts in large volumes makes it an essential process in modern manufacturing. At S.B. Weston our experienced team of plastic moulding designers and engineers can help you understand the key steps and advantages of the injection molding process and how to utilise it to help you achieve a successful manufacturing project.
Contact Us for Expert Plastic Molding Advice!
Why not get in touch and arrange a free, no obligation design consultation where members of our experienced team can look at your project’s exact requirements and advise you how to best proceed. We’re happy to sign NDA’s to protect your product designs, so why not get in touch, we’d love to help make your project a British manufacturing success!